Excavator use Disassembly All-in-one Machine
Product advantages
Model | Unit | VS08C |
Product weight | kg |
1900 |
Max. opening | mm |
630 |
Length | mm |
2475 |
Width | mm |
760 |
Rotation method | 360° hydraulic | |
Pressure | bar |
320 |
Root shear force | t |
150 |
Central shear force | t |
106 |
Front end clamping force | t |
56 |
Suitable for excavator | t | 18-26 |
1. **Powerful Dismantling:** The auto Dismantling Shear's robust design and hydraulic power allow it to easily break down and dismantle structures, vehicles, and other materials.
2. **Versatile Application:** This attachment is suitable for a wide range of tasks, including demolition of buildings, vehicle scrapping, and handling bulky debris.
3. **Precision Control:** The hydraulic system ensures precise control over the grapple's movement, allowing operators to navigate through intricate dismantling tasks with accuracy.
4. **Secure Grip:** The grapple's strong jaws provide a secure and stable grip on objects, preventing slippage during lifting and manipulation.
5. **Efficiency:** By streamlining the dismantling process, the auto Dismantling Shear enhances operational efficiency and reduces labor time.
6. **Safety:** With its remote operation capability and advanced control features, the grapple enhances operator safety by minimizing direct contact with potentially hazardous materials.
In summary, the auto Dismantling Shear is an essential attachment for efficient and controlled demolition and dismantling operations, offering versatility, precision, and enhanced safety for excavator-based tasks.
Design advantage
1. Special rotary support is used, which is flexible in operation, stable in performance and high in torque.
2. The shear body adopts imported HARDOX400 sheet, which has high strength and high shear force.
3. The blades are made of imported materials and have a longer life span.
4. The pressure clamp arm is fixed to the disassembled vehicle from three directions to facilitate the disassembly of the disassembly scissors.
5. Disassembly shears with pressure clamp arms can quickly disassemble all kinds of scrapped vehicles.
product display
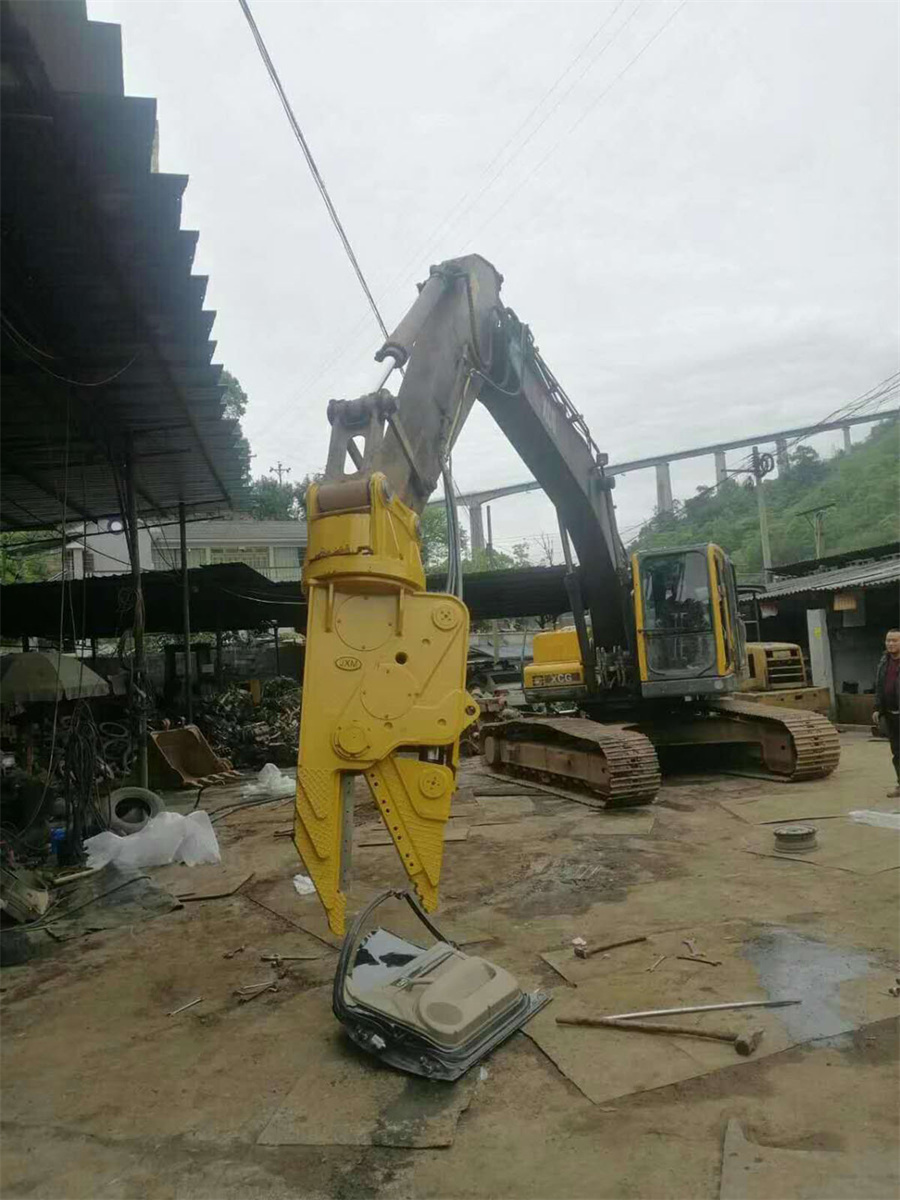
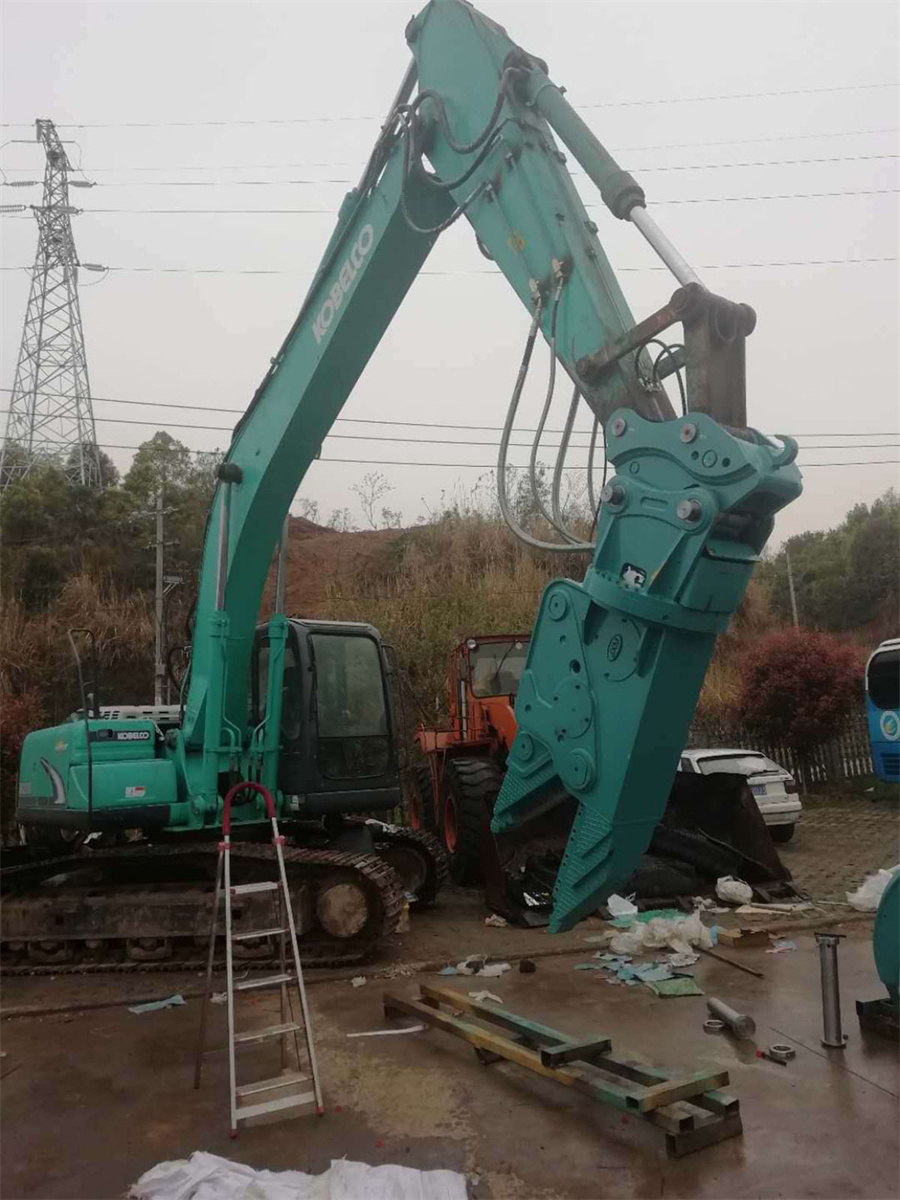
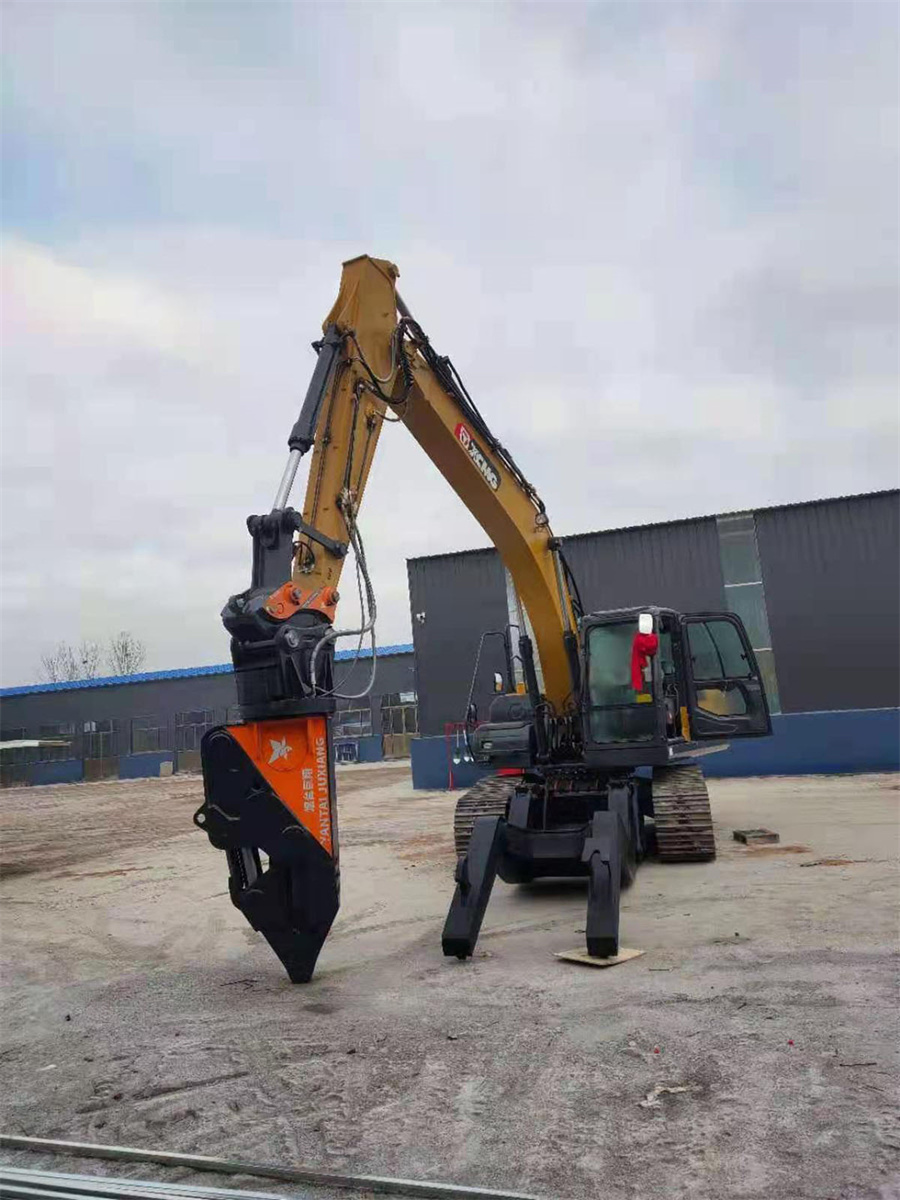
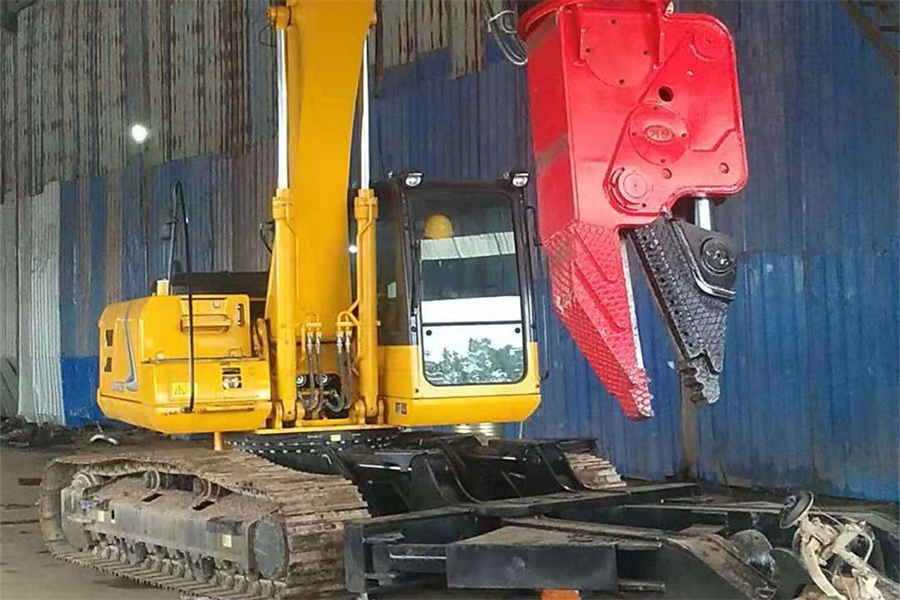
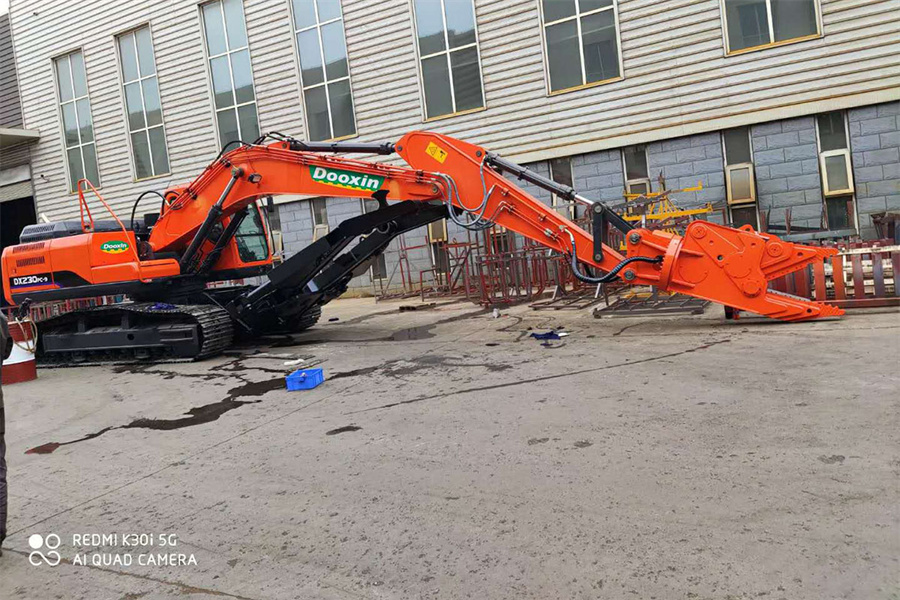
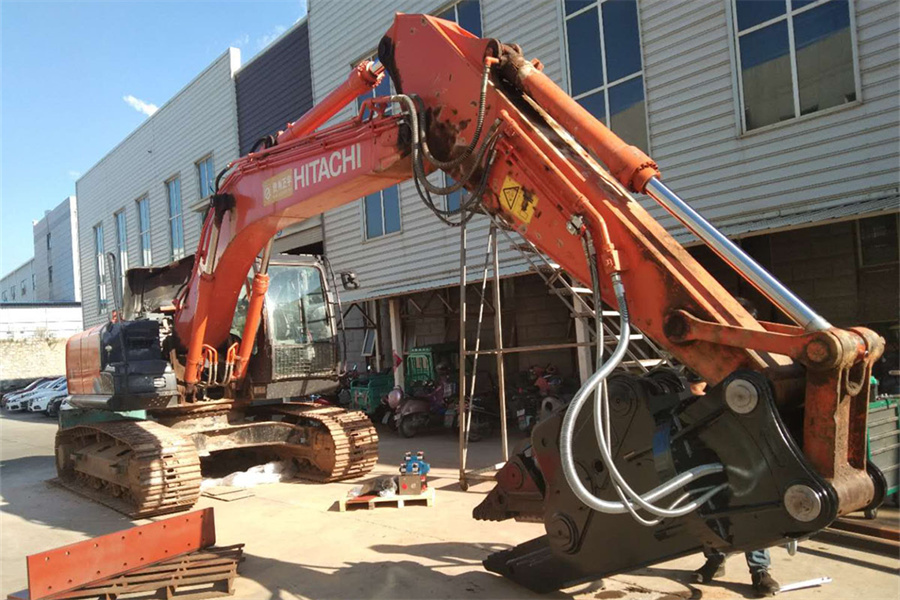
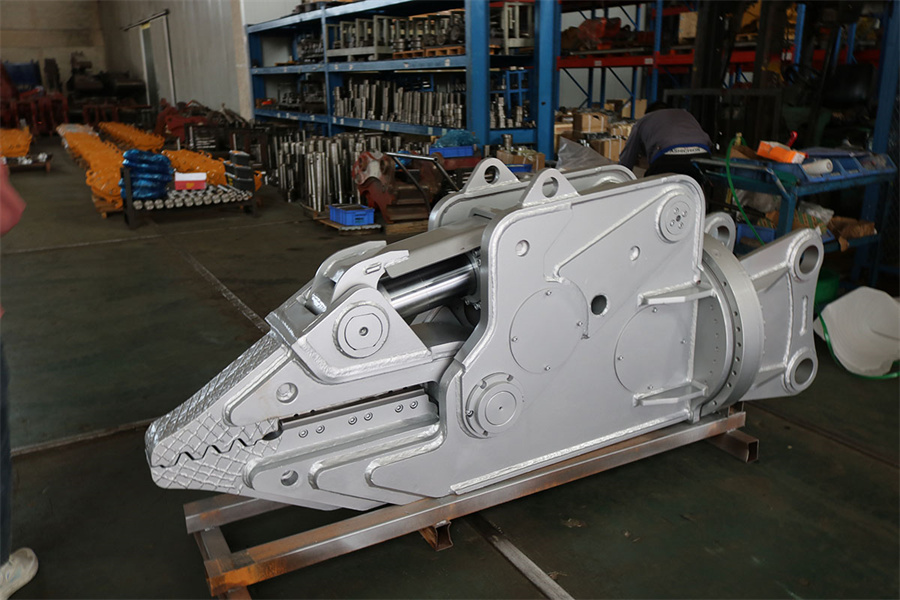
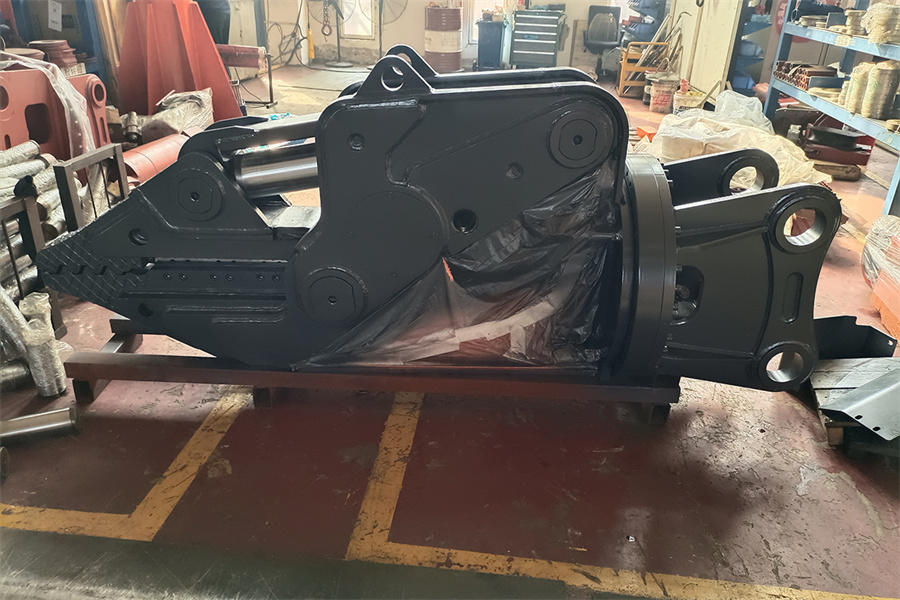
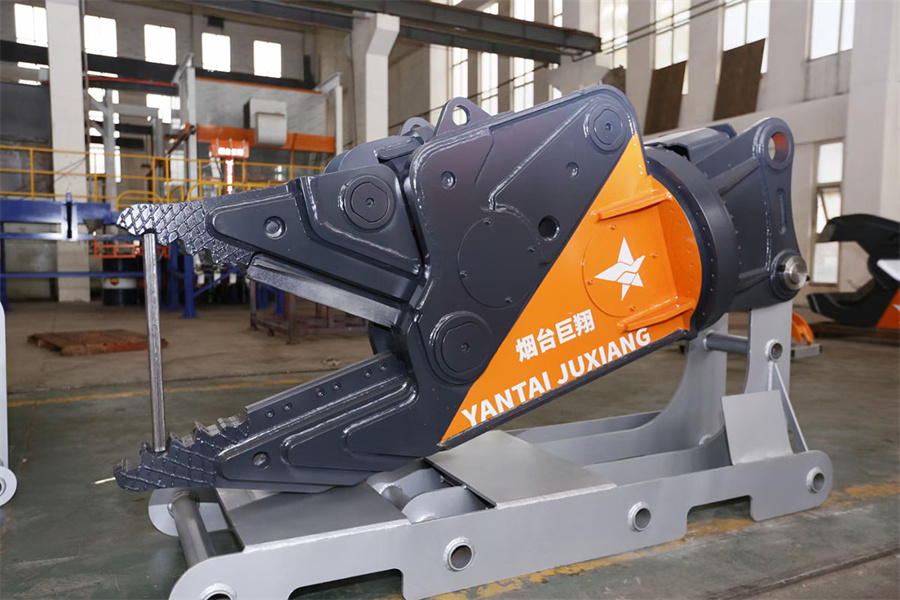
Applications

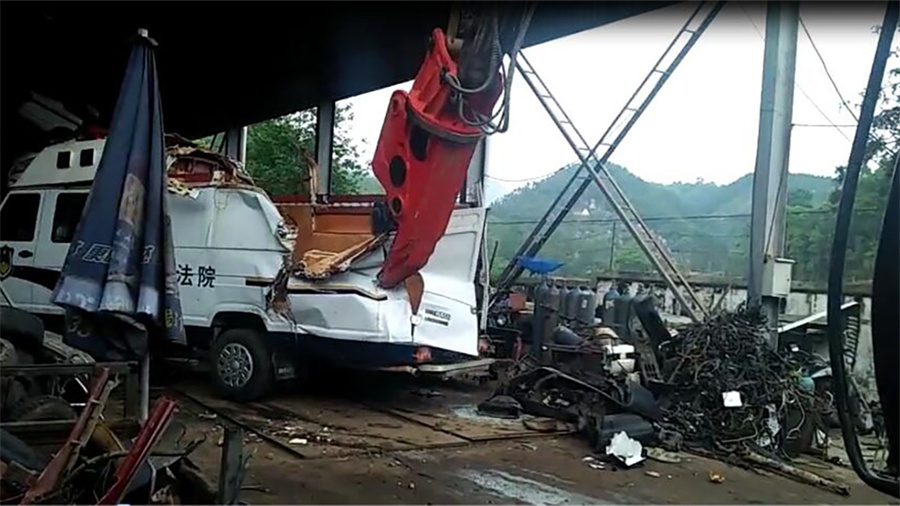
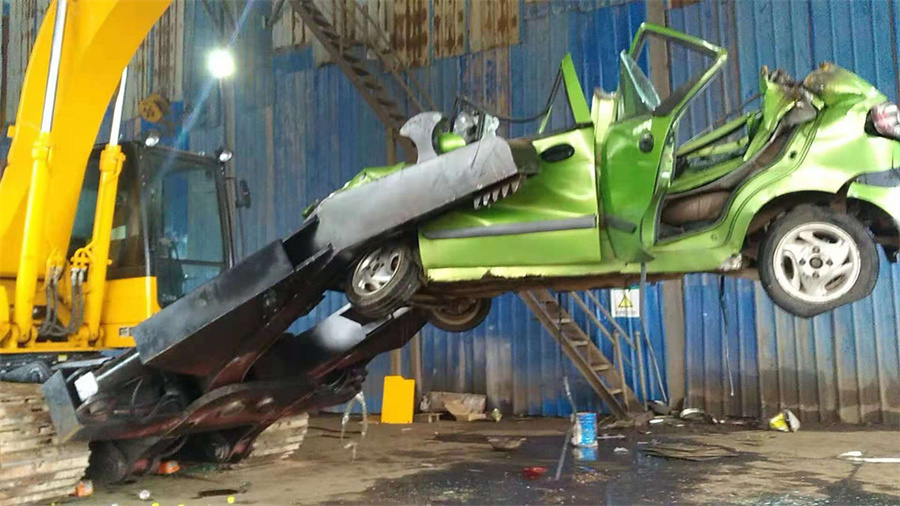

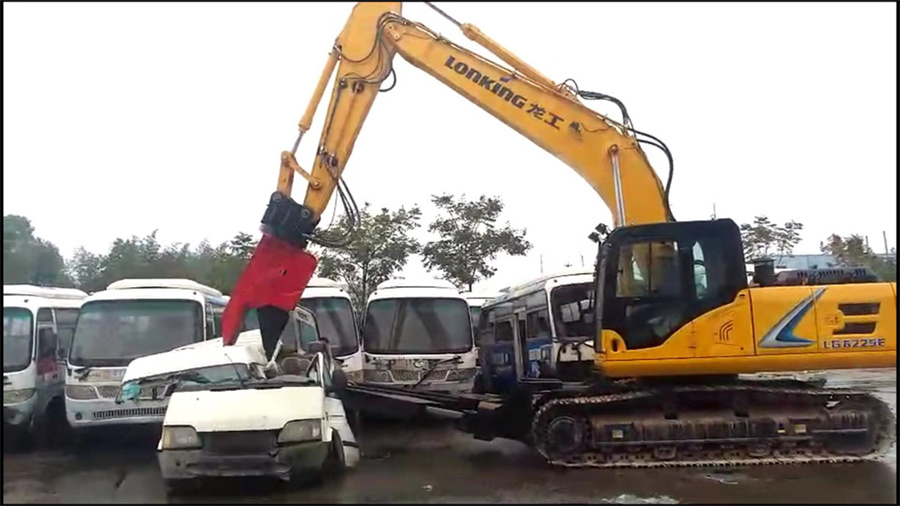
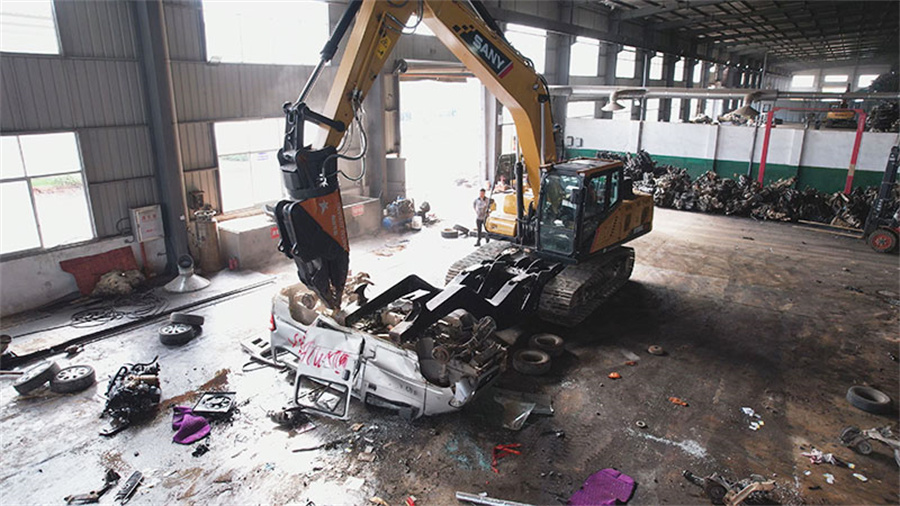
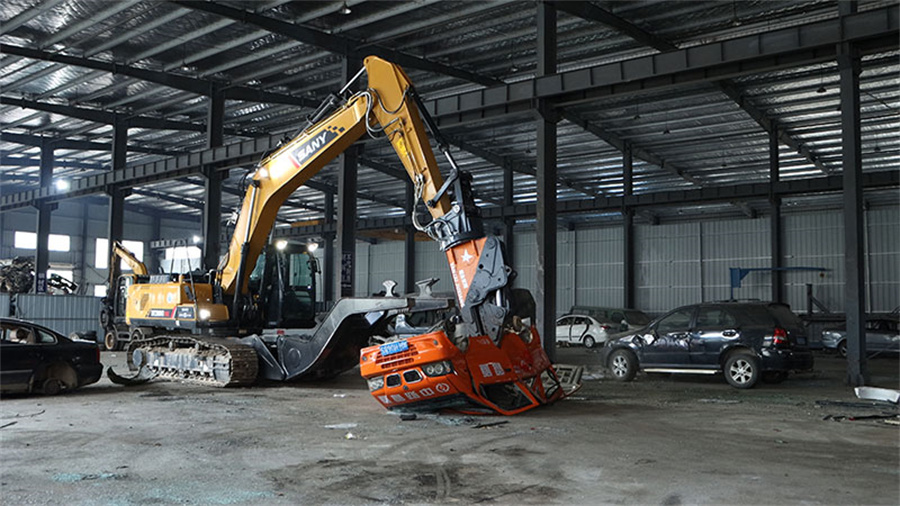
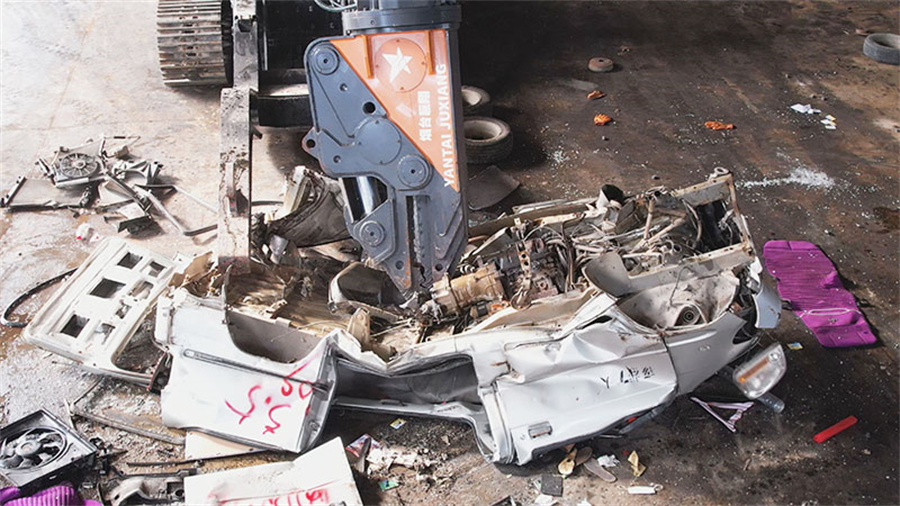
Our product is suitable for excavators of various brands and we have established long-term and stable partnerships with some well-known brands.
About Juxiang
Accessoryname | Warrantyperiod | Warranty Range | |
Motor | 12 months | It is free to replace the cracked shell and broken output shaft within 12 months. If the oil leakage occurs for more than 3 months, it is not covered by the claim. You must purchase the oil seal by yourself. | |
Eccentricironassembly | 12 months | The rolling element and the track stuck and corroded are not covered by the claim because the lubricating oil is not filled according to the specified time, the oil seal replacement time is exceeded, and the regular maintenance is poor. | |
ShellAssembly | 12 months | Damages caused by non-compliance with operating practices,and breaks caused by reinforce without the consent of our company,are not within the scope of claims.If Steel plate cracks within 12 months,the company will change the breaking parts;If Weld bead cracks,please weld by yourself.If you are not capable to weld,the company could weld for free,but no other expenses. | |
Bearing | 12 months | The damage caused by poor regular maintenance, wrong operation, failure to add or replace gear oil as required or is not within the scope of claim. | |
CylinderAssembly | 12 months | If the cylinder barrel is cracked or the cylinder rod is broken, the new component will be replaced free of charge. The oil leakage occurring within 3 months is not within the scope of claims, and the oil seal must be purchased by yourself. | |
Solenoid Valve/throttle /check valve /flood valve | 12 months | The coil short-circuited due to external impact and the incorrect positive and negative connection is not in the scope of claim. | |
Wiring harness | 12 months | The short circuit caused by external force extrusion, tearing, burning and wrong wire connection is not within the scope of claim settlement. | |
Pipeline | 6 months | Damage caused by improper maintenance, external force collision, and excessive adjustment of the relief valve is not within the scope of claims. | |
Bolts, foot switches, handles, connecting rods, fixed teeth, movable teeth and pin shafts are not guaranteed; The damage of parts caused by failure to use the company’s pipeline or failure to comply with the pipeline requirements provided by the company is not within the scope of claim settlement. |
1. When installing a pile driver onto an excavator, make sure the excavator’s hydraulic oil and filters are replaced after the installation and testing. This ensures the hydraulic system and parts of the pile driver work smoothly. Any impurities can damage the hydraulic system, causing issues and reducing the machine’s lifespan. **Note:** Pile drivers demand high standards from the excavator’s hydraulic system. Check and repair thoroughly before installation.
2. New pile drivers need a break-in period. For the first week of use, change the gear oil after half a day to a day’s work, then every 3 days. That’s three gear oil changes within a week. After this, do regular maintenance based on working hours. Change the gear oil every 200 working hours (but no more than 500 hours). This frequency can be adjusted depending on how much you work. Also, clean the magnet each time you change the oil. **Note:** Don’t go longer than 6 months between maintenance.
3. The magnet inside mainly filters. During pile driving, friction creates iron particles. The magnet keeps the oil clean by attracting these particles, reducing wear. Cleaning the magnet is important, about every 100 working hours, adjusting as needed based on how much you work.
4. Before starting each day, warm up the machine for 10-15 minutes. When the machine has been idle, oil settles at the bottom. Starting it means the upper parts lack lubrication initially. After about 30 seconds, the oil pump circulates oil to where it’s needed. This reduces wear on parts like pistons, rods, and shafts. While warming up, check screws and bolts, or grease parts for lubrication.
5. When driving piles, use less force initially. More resistance means more patience. Gradually drive the pile in. If the first level of vibration works, there’s no need to rush with the second level. Understand, while it might be quicker, more vibration increases wear. Whether using the first or second level, if pile progress is slow, pull the pile out 1 to 2 meters. With the pile driver and excavator’s power, this helps the pile go deeper.
6. After driving the pile, wait 5 seconds before releasing the grip. This reduces wear on the clamp and other parts. When releasing the pedal after driving the pile, due to inertia, all parts are tight. This reduces wear. The best time to release the grip is when the pile driver stops vibrating.
7. The rotating motor is for installing and removing piles. Don’t use it to correct pile positions caused by resistance or twisting. The combined effect of resistance and the pile driver’s vibration is too much for the motor, leading to damage over time.
8. Reversing the motor during over-rotation stresses it, causing damage. Leave 1 to 2 seconds between reversing the motor to avoid straining it and its parts, extending their life.
9. While working, watch for any issues, like unusual shaking of oil pipes, high temperatures, or odd sounds. If you notice something, stop immediately to check. Small things can prevent big problems.
10. Ignoring small issues leads to big ones. Understanding and caring for equipment not only reduces damage but also costs and delays.